- There are no more items in your cart
- Shipping Free
- Total €0.00
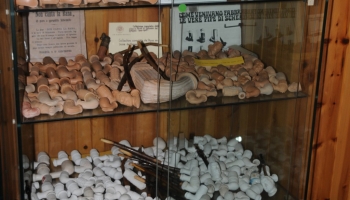
The clay pipes
Published : 06/20/2019 11:30:34 - Categories : Pipe
The history of pipes, from their origin to the present day, has yet to be written. A separate chapter, and probably the most interesting and important, has to be devoted to clay pipes.
Bassano Del Grappa, situated in the province of Vicenza, one of the most beautiful cities of Italy, is renowned for its grappa, its pottery and its ancient bridge called “Ponte degli Alpini”. It also was the most famous city for the production of clay pipes in Europe. The origins of clay pipe production date back to 1600-1700; the first producers were the people of Bassano Del Grappa who were already experts in modeling clay for ceramics.
The art of pipe making developed along with pipe development and demand from Italy and from France, Germany, England, etc. The first pipe makers were the English, the Spanish and the Sardinians, followed by the Dutch, the Germans and the French. In these countries pipe models generally didn't vary much from the typical Corsair or Genovese shape, characterized by the “pinchetto”, a “heel” under the bowl.
The first French pipes were produced in Dunkerque in the first half of the 17th century; then the city of Rouen started its production in 1663; in 1785 famous Dieppe pipes were made by a certain “Monsieur Bretel”.
As the Gambier was the most famous pipe in France, so were the pipes of Bassano in Italy, due to both the quality and the quantity of pipes produced. Gambier opened in 1780 in Givet, at the foot of Mount D'Haurs; development occured in 1894, when its catalog offered nearly 2,000 models. In Bassano the pipe sector started developing in 1860, when the pipes of Bassano were requested worldwide, as well as nationwide. The prestige, the variety of models and the manufacturing system were completed by Giuseppe Reatto, who independently continued the production of the pipes of Bassano in his house in via S.S. Trinità, now a listed building, where his wife Maria Reatto still lives (production stopped in 1968 after the death of Mr. Reatto) She is considered the only living person on earth who has perfect knowledge of the ancient art of making clay pipes.
In her house Maria Reatto keeps all the bronze molds and all the models that were produced by her husband; among the numerous molds the most famous is the one reproducing a pipe-shaped St. Mark's Campanile in bronze; it weighs more than 15kg.The Reatto factory made both French models (Marseilles, Gambier, the Americans, the Samantha) and Chemnitz pipes, of which molds in perfect conditions to be used again still exist. Reatto used to manufacture: Marseilles, Napoletane, Chioggiotte, Romagnole, Abruzzesi, Ferraresi, Lorenzo Stecchetti, “Non canta la Rana” (the Raganella came long after), Salutare, etc.
One more detail: Reatto used to supplied with Chemnitz models the German, Italian and French market, as far as the Cossacks of Tsar Nicholas Romanov.
Below we quote an interview with Mrs. Maria Reatto.
«My husband Giuseppe Reatto (Bepi) took over a small laboratory that produced clay pipes and in few years he developed and perfected his work until he gained a reputation that went beyond national boundaries, exporting our pipes to practically each country of the world. I still conserve commercial correspondence, copies of orders, invoices, etc, of clients from every European country, America, Egypt, Israel, and so on. The models we used to produce were more than 160 and each of them had, along with its identification number, its own name, generally given by the city it was destined to: Romagnola, Chioggiotta, Abruzzese, Marsigliese...Pipes were made both in red and white clay, and in real Chemnitz, that my husband used to order directly from Germany. For the whole 35 years I've been here, we never ordered that anymore; I once found in a hole a great number of Chemnitz pipes that we threw all away.
The white clay used for the Chioggiotte was picked up here in Bassano, behind the S.S. Trinità church's farms, where nothing grew but “visele” (grapevine). We dug till we found suitable ground for our work; when we couldn't find any more we started digging somewhere else. The clay we excavated was placed in a dedicated hole and then was worked, milled and filtered. Red clay came from the hills of Romano; to mix it well, it was combined with some of our white clay and placed in a separate hole (it was drawn out with a pump).
When the mixture had a certain consistency it was mixed by hand and balls, as big as a loaf, were thrown with vim against a dedicated brick wall; the mixture stuck to the bricks, which absorbed the water.
A man in charge of this work turned these mixtures. His job was exclusively to throw the “loaves” of clay against the wall; the clay was then placed in a large storage room (in a hole) and kept ready for processing; in dry temperatures it was kept wet with some water to make the mixture right for modeling. The clay was put in a tool called “bigolaro”that pressed it and gave it the shape of a tube; by hand it was cut to the an appropriate length to produce a pipe and put into a bronze mold. The molds were composed of two identical halves; when clay was in one half of the mold, the other half was superimposed and the mold was placed into a special vise and pressed. Then, always by hand, two “broli” were placed, one into the shank and the other one into the bowl (both the molds and the “broli” were first anointed with a solution of olive oil and naphtha). The pipe removed from the mold was hung on a board with nails (a nail for each pipe) and left there to dry. When it was dry but still soft, the pipe was refined with an appropriate iron near the junction of the mold.
The clay pipes were put in our oven by the thousands; in the lower part heat was stronger and after 10 hours of uninterrupted warmth, as we saw the oven reach 900°C, we checked the warning light and if it was red, that meant the pipes weren't fired yet and we used the regulator to push the heat where it was needed most.
After approximately 18 hours of fire, we let it go out and closed the regulator so that if any pipe wasn't completely fired, it could still bake. Then they were left to cool down and the following day, usually on Monday, the oven was opened and the fired pipes were removed. The register was opened so that the workers found the goods ready for packing; breakage didn't even reach 1%. I'd like to say a few words about the black clay pipes. The process and firing were both secret, since my husband had perfected the whole process to the utmost.
Everything consisted in the firing: the pipes were laid in iron containers, a layer of sawdust first, then a layer of pipes, then again a layer of sawdust and one of pipes and so on until the container was full. It was then hermetically sealed with a cap and some fire clay. Once the oven had cooled, the container was removed and the pipes were perfectly black.»